Manufacturing service for customized stainless steel bodies and chassis
CTT has over 10 years of experience in the production of mid- and full-size bus and passenger car bodies and chassis. CTT has a comprehensive capability of engineering, processing and assembly as a "one-stop" service. Frame is the main support structure of a vehicle, connecting all parts of the vehicle. Fully engineered frame products provide the best solutions for customers by adopting a variety of manufacturing and assembly technologies.
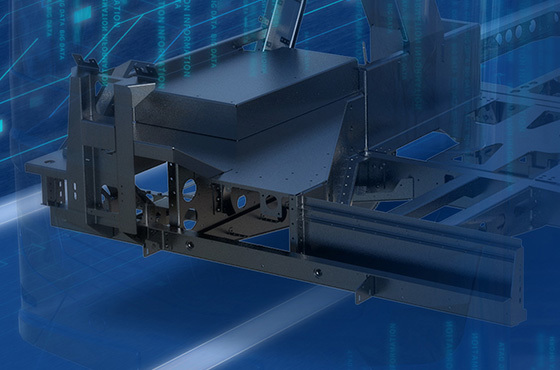
Complete body and parts
Technical expertise in various product and process areas.
Under the skin of each vehicle is the core structure of the vehicle, including the frame longitudinal beam, floor, upper body column and body side rails. By using innovative and high strength materials and manufacturing processes, CTT is constantly developing body structures that meet or exceed our customers' requirements for lightweight and crash performance.
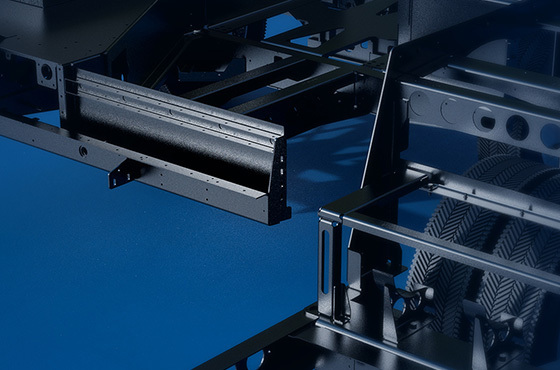
The world's leading chassis quality
CTT is a market leader in the field of chassis. We use a variety of innovative metal forming processes to meet the specific requirements of our customers, including hydroforming, roll forming, casting, stamping and bending. Integral engine frames and subframes are one of the core products provided by CTT. We use advanced coating technology to develop modular and flexible designs for different regions and products, improving corrosion resistance.
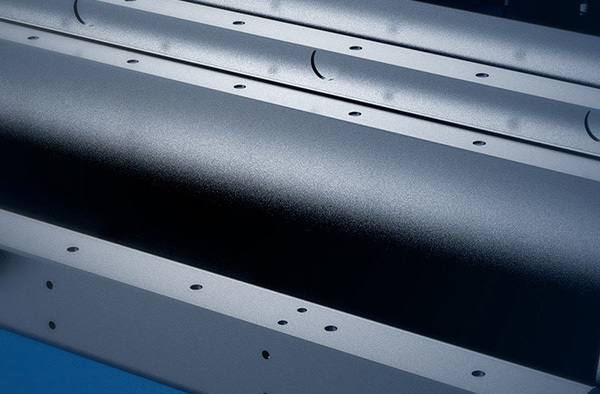
Stainless steel material advantage
The use of high-strength stainless steel in the passenger car frame instead of carbon steel components, weight reduction of 34%, tooling investment decreased by 30-40%, and corrosion resistance. The technology is mainly used for the sub-frame, but can also be applied to a variety of bodies and chassis to reduce weight.
● Cost reduction: minimize material and manufacturing costs
● Durability: long service life, low life cycle cost
● Impact resistance: with high strength and high impact resistance
● Lightweight: minimize the weight of the structure
Design And Development Capability
Product Design And Development Plays An Important Role In Market Success.
With A Perfect Research And Development System And Efficient Transformation Of Innovative Technology Production Mode, With Strong Research And Development Design Ability, And Strictly Control The Development Process Of Each Link, To Ensure The Quality And Reliability Of Products.
In Terms Of The Body, We Offer Integrated Development Services Ranging From Preliminary Body Analysis And Body Index Assessment To Body Design. As For The Chassis, Our Expertise Extends From System Integration And Digital Design To Chassis Dynamics Analysis Modules. We Are Dedicated To Providing Tailored Solutions By Thoroughly Understanding Our Customers' Market Landscape And Technical Objectives. We Are Committed To Providing Quality Products And Services To Meet The Needs Of Customers And Future Development.
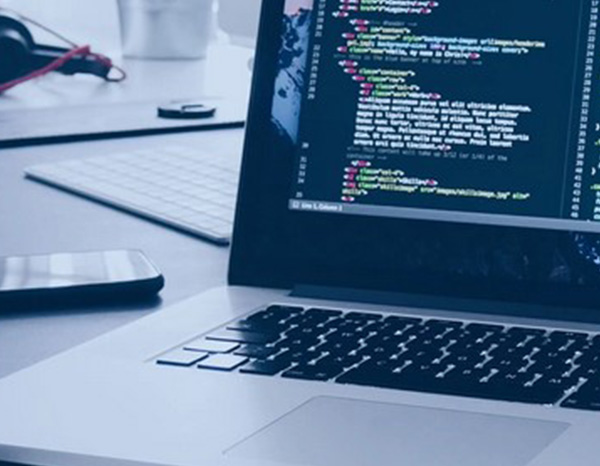
Manufacturing and testing capabilities
Prototyping and small-lot manufacturing
CTT has two modes of cooperation: ODM and OEM. The Prototype Plant produces concept cars, test cars and prototypes for all stages of the design process, as well as highly customized, small-batch finished cars and components. Our goal is to achieve mass production and proof of concept of new technologies at the prototype stage, and conduct road and off-road reliability tests and component tests of vehicles.
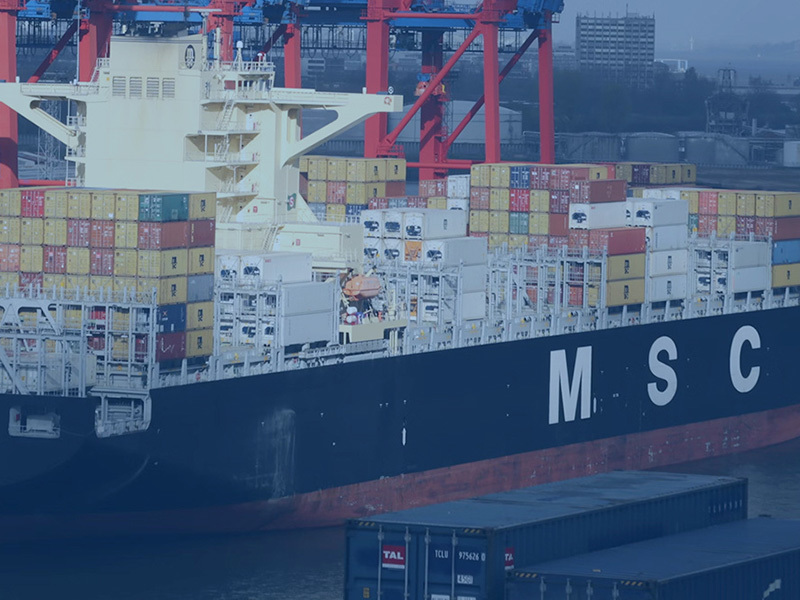
Fixtures/Fixtures and Automation
We offer everything from custom designs and fixtures to fully automated fixtures and robotic units, from overall positioning and clamping concepts to CAD design, assembly, measurement and adjustment. Our virtual feasibility testing, reusable standard fixtures and offline and online systems for robot programming can help you save time and costs.
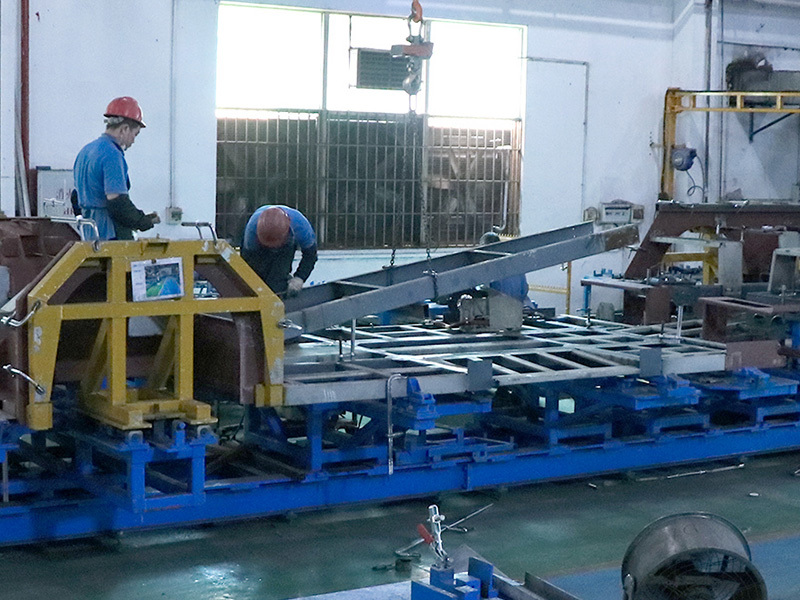
The body workshop
To ensure successful volume production, we manufacture prototypes with the highest quality. We have a wide range of joint technologies available for steel and lightweight joints used in existing automated units, including laser welding, self-piercing riveting, riveting, friction element welding, flow drilling and tightening, flow push, etc.We also offer custom manual processes and automation for prototype and small volume production.
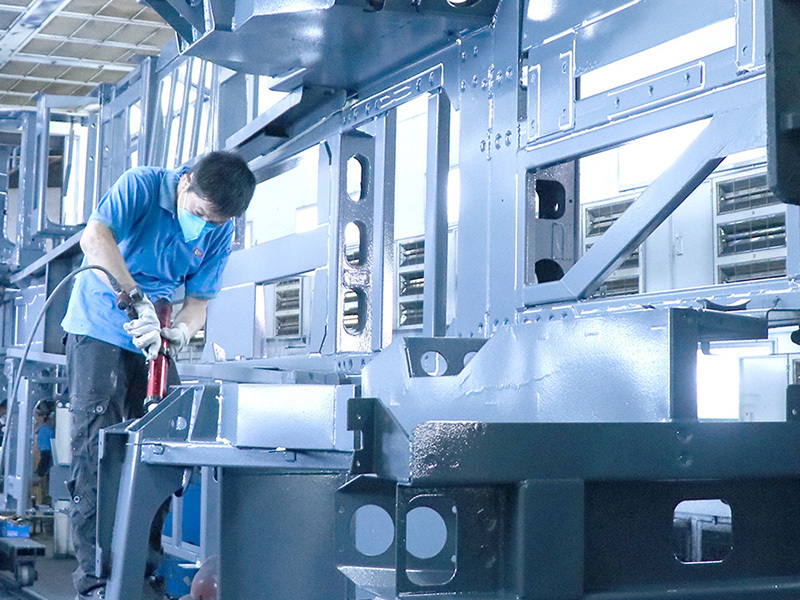
Logistics, maintenance, quality
We ensure that all parts are in the right place at the right time, and that the required parts are readily available at every stage of operation. Quality checks, detailed documentation and comprehensive records are maintained at every step of the process to ensure that everything fits together seamlessly.
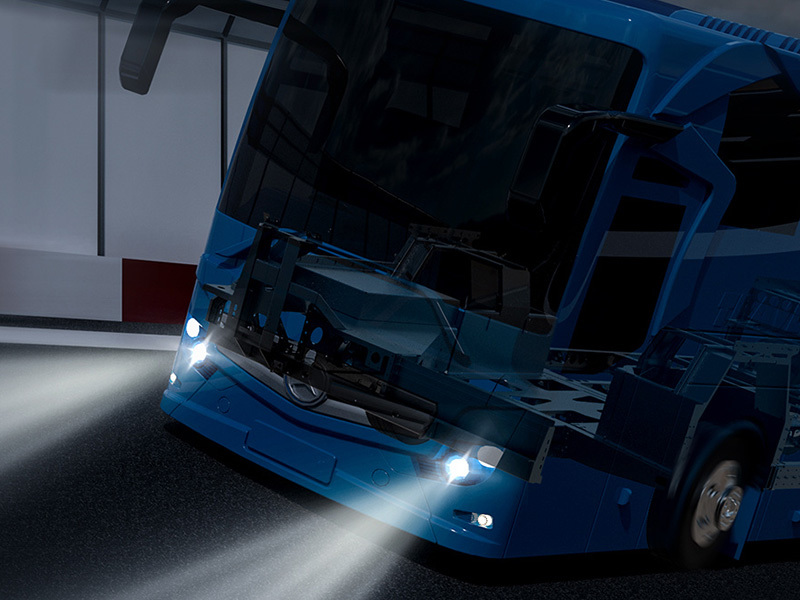
Parts testing, road and off-road vehicle reliability and misuse testing
Parts testing included static warping and torsion, door subsidence, angular stiffness and anti-concave stiffness tests. We developed test procedures, conducted road and off-road tests, performed misuse tests and recorded results.