Auto Chassis Metal Fab: Key Steps from Materials to Process
Release time:
2025-04-16
The sheet metal processing of automobile chassis involves material selection, key process steps and quality control. High-strength steel, aluminum alloy and zinc steel plate are common materials, among which high-strength steel is used for key load-bearing parts, aluminum alloy can reduce weight and achieve lightweight, and zinc steel plate can ensure rust-proof performance and extend service life.
In the field of automobile manufacturing, the chassis is a core component that carries the weight of the vehicle, transmits power and ensures driving stability. The quality of its sheet metal processing directly affects the safety, handling and durability of the vehicle. Automobile chassis sheet metal processing transforms raw materials into structural parts that meet complex mechanical performance requirements through precise processing of metal sheets. This article will systematically analyze the core points of automobile chassis sheet metal processing from the dimensions of material selection, key process steps, quality control, etc.
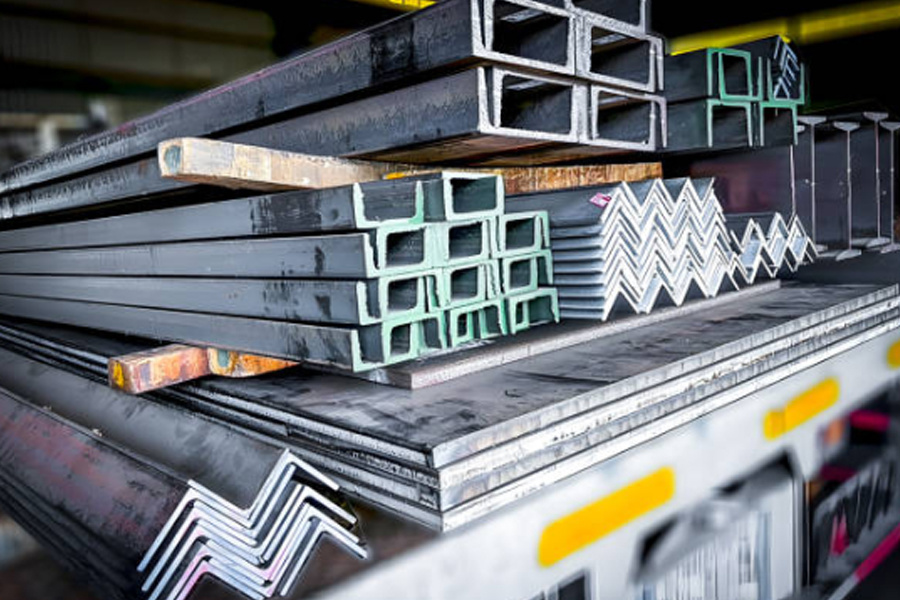
Material selection: the core consideration of balancing strength and lightness
The material selection for automobile chassis sheet metal processing needs to balance high strength, lightness and processing adaptability. Common materials include:
1. High-strength steel
High-strength steel (such as dual-phase steel and hot-formed steel) has become the preferred material for key load-bearing components of the chassis (such as longitudinal beams and cross beams) due to its high tensile strength and strong deformation resistance. Its yield strength is usually higher than that of ordinary steel, which can effectively resist the impact force and alternating load during driving. At the same time, through reasonable cross-section design, it can reduce the amount of material while ensuring structural strength and achieve the goal of lightweight.
2. Aluminum alloy
Aluminum alloy is widely used in chassis suspension system components (such as control arms and steering knuckle brackets) due to its low density, high specific strength and good corrosion resistance. Through heat treatment process optimization, aluminum alloy parts can meet the performance requirements of complex stress scenarios, while significantly reducing chassis weight, improving vehicle fuel efficiency and handling flexibility.
3. Galvanized steel sheet
Galvanized steel sheet has good anti-rust performance due to its surface coating. It is often used for non-critical chassis parts that need to be exposed to humid environments for a long time (such as chassis guards and spare tire brackets). While ensuring basic mechanical properties, it extends the service life of the parts.
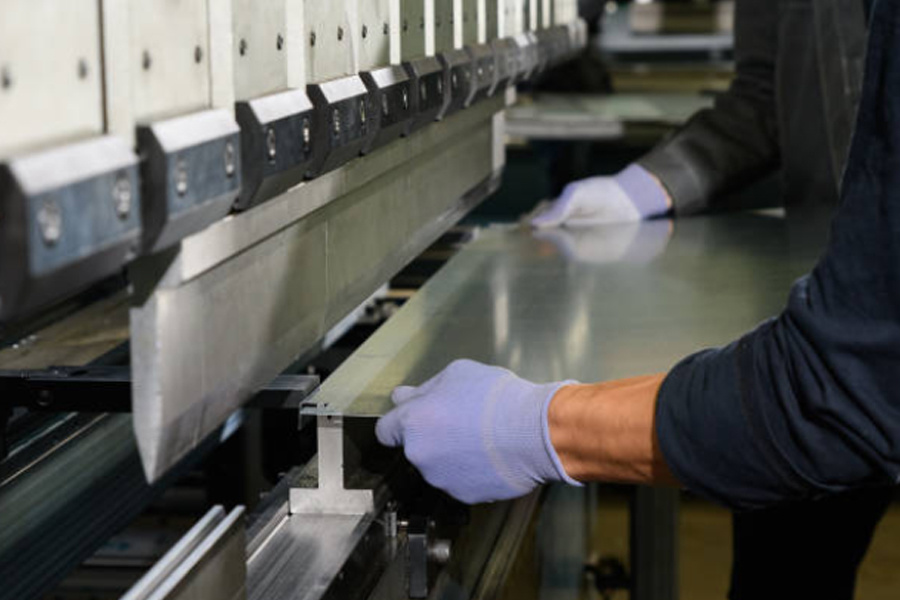
Key process steps: Precision processing to ensure performance realization
1. Cutting and blanking: basic control of dimensional accuracy
Cutting is the first process of chassis sheet metal processing, mainly using CNC laser cutting or CNC punching technology. CNC laser cutting melts the sheet through a high-energy laser beam, which can achieve complex contour processing with millimeter-level accuracy. It is suitable for a variety of materials such as high-strength steel and aluminum alloy, especially for the cutting of special-shaped structural parts. CNC punching machines complete batch blanking through die stamping, which is highly efficient and suitable for the processing of regular-shaped parts. Both processes require adjusting parameters according to material properties to ensure that the cuts are smooth and burr-free, laying the foundation for subsequent processes.
2. Bending: Precise shaping of three-dimensional structures
The bending process uses a CNC bending machine to apply pressure to the cut sheet to form a bending structure with a specific angle. In view of the complex geometric requirements of chassis components, it is necessary to combine 3D modeling software for bending path planning, accurately calculate parameters such as bending radius and springback, and avoid assembly problems caused by forming errors. For materials with higher hardness such as high-strength steel, hot bending processes are often used to reduce the yield strength of the material by heating, thereby improving forming accuracy and efficiency.
3. Welding connection: key enhancement of mechanical properties
Welding is the core process for connecting multiple components into a complete structure in chassis sheet metal processing. Common methods include:
● Resistance welding: suitable for thin plate welding, which connects welds by electrode pressure and current heating. It has high efficiency and small deformation, and is commonly used in the splicing of chassis covers.
● Carbon dioxide gas shielded welding: suitable for welding of medium and thick plates. The shielding gas can effectively prevent the oxidation of the weld and improve the connection strength. It is mostly used for welding chassis frame structures.
● Laser welding: With its high-precision and deep-penetration welding characteristics, it can achieve high-quality connection of lightweight materials such as aluminum alloys, reduce welding deformation, and meet the connection requirements of lightweight chassis components. During the welding process, the welding parameters (such as current, voltage, and welding speed) must be strictly controlled, and post-weld flaw detection must be performed to ensure that the weld strength meets the performance requirements of the parent material.
4. Surface treatment: Double improvement of protection and beauty
Surface treatment is a key link in enhancing the corrosion resistance of chassis components. The main processes include:
● Spraying: A paint coating is formed on the surface of the component through electrostatic spraying or dipping, which can effectively resist external erosion such as rainwater and mud, while providing a variety of appearance options.
● Galvanizing: A zinc layer protective film is formed on the surface of the steel using hot-dip galvanizing or electro-galvanizing processes. It is suitable for components that are exposed to humid environments for a long time to improve rust resistance.
● Anodizing: For aluminum alloy parts, an oxide film is generated on the surface through electrochemical methods to enhance corrosion resistance and wear resistance. At the same time, dyeing can be performed to meet appearance requirements.
Automobile chassis sheet metal processing is a systematic project that integrates material science, mechanical engineering and precision manufacturing. Every link from material selection to process implementation directly affects the performance of chassis parts and the quality of the whole vehicle. Choosing a processing service provider with professional technology, advanced equipment and strict quality control can provide automobile manufacturers with reliable chassis parts solutions and help improve the market competitiveness of vehicles.
Key Words