The road to innovation for the leading enterprise in the intelligent manufacturing of precision parts
Release time:
2025-06-17
Chuntian Machinery Technology has built a closed loop of precision manufacturing through a full-chain collaborative system, achieving stable control of the dimensional tolerance of key parts within the range of ±0.02mm, and the product yield has exceeded 99.8%, an industry high. Intelligent manufacturing enables global layout, builds a digital flexible production system, and realizes efficient collaboration of the global supply chain.
In the wave of intelligent transformation of the global manufacturing industry, the precision parts industry is becoming the core battlefield of technological innovation. As a leading enterprise in this field, Zhuhai Chuntian Machinery Technology Co., Ltd. has deeply integrated intelligent manufacturing technology into the precision processing link by building a full-chain collaborative system of "R&D-production-sales", forming a digital closed loop from material processing to finished product delivery. Relying on the independently developed CBS business system management platform, the company has realized real-time monitoring and process optimization of production data. The precision transmission parts, high-precision medical components and other products it has developed have reached the international leading level in tolerance control and surface treatment technology. By building a warehousing network and regional technology centers covering Europe, America and Southeast Asia, Chuntian has not only accelerated the global application of local innovation results, but also established technical barriers in strategic fields such as new energy equipment and medical equipment, providing a practical model for the "high-end, intelligent and green" goals proposed in the Made in China 2025 strategy.
New benchmark for intelligent manufacturing of precision parts
Relying on the independently developed high-precision processing technology system and intelligent production line configuration, Chuntian Machinery Technology has built a precision manufacturing closed loop covering the entire process. By introducing five-axis linkage machining centers, nano-level detection equipment and AI-assisted process optimization systems, the company has achieved stable control of the dimensional tolerance of key components within the range of ±0.02mm, and the product yield has exceeded 99.8%, an industry high. In the field of core components of automotive fuel injection systems, the modular precision valve body developed by Chuntian has successfully replaced imported products, helping the domestic supply chain to achieve independent control of key links. With the dual support of AS9100 aerospace quality management system certification and IATF16949 automotive industry standards, its developed titanium alloy medical joint components have passed FDA clinical verification, demonstrating cross-industry technology migration capabilities. This innovative model that integrates precision machining, intelligent monitoring and cross-domain collaboration is redefining the value benchmark of China's high-end manufacturing.
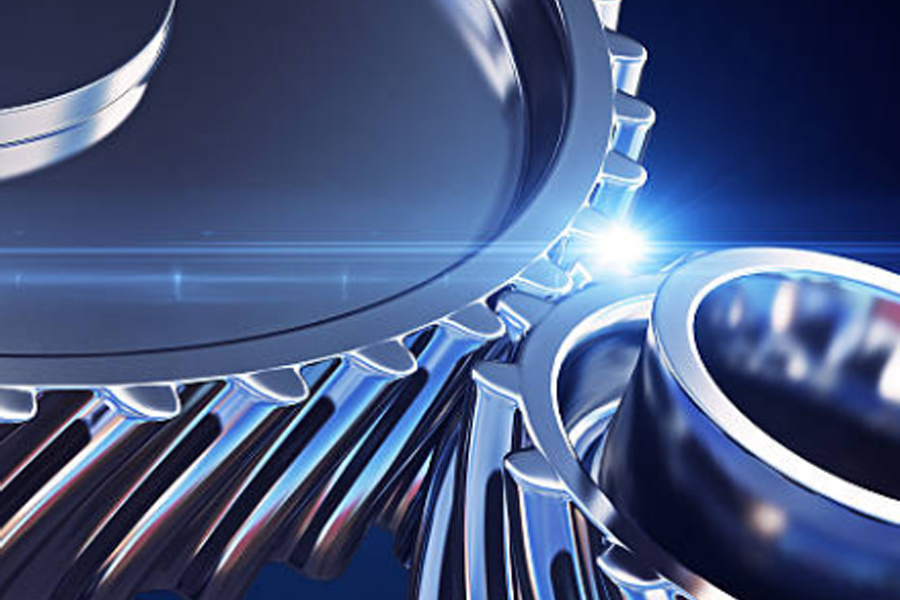
Intelligent manufacturing empowers global layout
By building a digital flexible production system, Chuntian Machinery Technology has achieved efficient collaboration in the global supply chain. Relying on the self-developed CBS business system management platform, the company has deeply embedded industrial Internet of Things technology into the manufacturing process, built 12 intelligent production lines in the Pearl River Delta headquarters base, and the digital coverage rate of key processes reached 92%. Through the real-time linkage between the intelligent warehousing system and the logistics nodes in North America and Europe, the order response cycle is shortened to 60% of the industry average, supporting a just-in-time delivery network covering 28 countries and regions. It is worth noting that the technical service center established by the company in Southeast Asia remotely guides equipment operation and maintenance through the digital twin system, which improves the efficiency of equipment troubleshooting for overseas customers by more than 40%. This operation model based on intelligent manufacturing not only strengthens the local R&D advantages, but also realizes the precise coordination of global branches through the data-driven decision-making system, providing a replicable international development path for the implementation of the Made in China 2025 strategy.
Innovative Practice of Made in China 2025
In the process of implementing the national "Made in China 2025" strategy, enterprises build core competitive advantages through digital transformation and intelligent upgrading. Relying on the independently developed CBS business management system, the data of the entire production process is connected, and the order response efficiency is improved by more than 40%. Through the intelligent manufacturing platform certified by the integration of information and industrialization management system, the equipment networking rate is increased to 92%, forming a closed loop of quality traceability. As a provincial engineering technology research center, the ultra-precision machining technology it developed broke through the 0.005mm tolerance control bottleneck and reached the international advanced level in the field of medical implant manufacturing. In the construction of the technology innovation system, it established a joint laboratory with universities such as South China University of Technology, completed the transformation of 5 core patents, involving new material applications and surface treatment process innovation, and significantly improved the stability of products under extreme working conditions. This innovation model based on intelligent equipment and driven by industry-university-research collaboration is reshaping the value chain of the precision parts industry.
Internationalization strategy and innovation system
In the context of global industrial collaboration, Chuntian Machinery Technology has built an international strategic core framework through the "R&D-Manufacturing-Service" trinity innovation system. Relying on the warehousing network and localized service centers in North America, Europe and Southeast Asia, the company has realized a 24-hour rapid response mechanism, significantly improving the resilience of the cross-border supply chain. The CBS business system management platform, which is promoted simultaneously, deeply integrates the lean production concept with digital tools, enabling 7 manufacturing bases distributed in three continents to share process parameters and communicate quality data. In order to strengthen its technical discourse power, the company has built a research and development matrix with the Guangdong Stainless Steel Engineering Technology Research Center as the core, investing 8% of its annual revenue in original technology research in the fields of precision machining, material modification, etc., and has obtained 56 international patent authorizations in total. This dual-track model of "technology-driven + localized operation" not only supports in-depth collaboration with global giants such as DANAHER and KOHLER, but also makes the "Chuntian Standard" gradually become a common practice in the field of high-end manufacturing through 12 international certification systems such as IATF16949.
By deeply integrating the intelligent manufacturing of precision parts with intelligent manufacturing, the company has built a full-link innovation system that runs through R&D, production and service. The "Chuntian Intelligent Manufacturing" model supported by a digital management platform not only realizes the refined control of production processes, but also effectively shortens the response cycle of the international market through the coordinated operation of a global warehousing network and a localized service team. This three-dimensional layout of "technology research and development + standard output + regional penetration" not only reflects the practical interpretation of the Made in China 2025 strategy, but also provides a replicable innovation paradigm for equipment manufacturing companies to explore global competition. In the process of continuously strengthening the integration of industrialization and information technology and the reserve of intellectual property rights, enterprises are gradually transforming from single product suppliers to industry solution designers. This role evolution may redefine the positioning coordinates of Chinese precision manufacturing companies in the global value chain.
Key Words